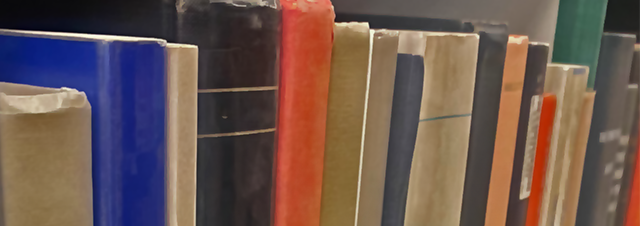
Faculty Publications
Sustainability Analysis Of Machining Inconel 718 Using Graphene-Based Nanofluids And Self-Lubricating Tools
Document Type
Article
Keywords
Carbon footprint, Economic analysis, Graphene, Inconel 718, Machining performance, Minimum quantity application, Sustainability
Journal/Book/Conference Title
Smart and Sustainable Manufacturing Systems
Volume
5
Issue
1
First Page
219
Last Page
241
Abstract
Inconel 718 has wide application due to its excellent strength at high temperatures and corrosion resistance. But because of the problems associated with machining, it is categorized as "hard-to-machine" material. The present work aims at identifying a sustainable method to machine Inconel 718 with the application of graphene. Sustainability evaluation consists of evaluating a product or process for the satisfaction of three E’s: employee, environment, and economy. In the present work, the effect of graphene-based cutting fluid and graphene-based self-lubricating tools on cutting forces and tool wear is evaluated while machining Inconel 718. In addition, economic analysis and carbon footprint analysis are carried out to verify the advantage and feasibility of using the formulated cutting fluids and self-lubricating tools. Furthermore, minimum quantity application of conventional cutting fluid and graphene-based nanofluids and dry machining using graphene-based self-lubricating tools are compared to estimate the best conditions for environmental impact. Minimum quantity application of 0.5 weight percent (wt %) graphene-based nanofluid showed the least tangential cutting forces, while 0.3 wt % showed the least tool wear. Tool wear decreased by ≈70–84 % with 0.3 wt % graphene-based nanofluid compared with dry machining over the velocity range of 65–115 m/min. At 112 m/min, the minimum quantity application of 0.3 wt % graphene-based nanofluid reduced carbon emission by 3,334 kg carbon dioxide compared with dry machining per machine tool per year. Minimum quantity application of 0.3 wt % graphene-based nanofluid is also found to be most economical compared with other environments at all cutting velocities showing ≈70–80 % reduction in expenditure compared with dry machining.
Department
Department of Applied Engineering and Technical Management
Original Publication Date
12-2-2021
DOI of published version
10.1520/SSMS20200036
Recommended Citation
Amrita, M.; Revuru, Rukmini Srikant; Siva, B.; and Kamesh, B., "Sustainability Analysis Of Machining Inconel 718 Using Graphene-Based Nanofluids And Self-Lubricating Tools" (2021). Faculty Publications. 5183.
https://scholarworks.uni.edu/facpub/5183