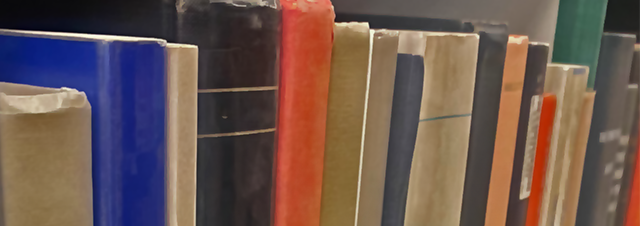
Faculty Publications
Wear Resistance Properties Of Austempered Ductile Iron
Abstract
A detailed review of wear resistance properties of austempered ductile iron (ADI) was undertaken to examine the potential applications of this material for wear parts, as an alternative to steels, alloyed andwhite irons, bronzes, and other competitive materials. Two modes of wear were studied: adhesive (frictional)dry sliding and abrasive wear. In the rotating dry sliding tests, wear behavior of the base material(a stationary block) was considered in relationship to countersurface (steel shaft) wear. In this wear mode, the wear rate of ADI was only one-fourth that of pearlitic ductile iron (DI) grade 100-70-03; the wear rates of aluminum bronze and leaded-tin bronze, respectively, were 3.7 and 3.3 times greater than that of ADI. Only quenched DI with a fully martensitic matrix slightly outperformed ADI. No significant difference was observed in the wear of steel shafts running against ADI and quenched DI. The excellent wear performance of ADI and its countersurface, combined with their relatively low friction coefficient, indicate potential for dry sliding wear applications. In the abrasive wear mode, the wear rate of ADI was comparable to that of alloyed hardened AISI 4340 steel, and approximately one-half that of hardened medium-carbon AISI 1050 steel and of white and alloyed cast irons. The excellent wear resistance of ADI may be attributed to the strain-affected transformation of high-carbon austenite to martensite that takes place in the surface layer during the wear tests.