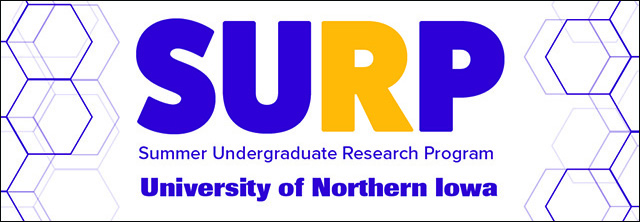
2024 Summer Undergraduate Research Program (SURP) Symposium
Location
John Deere Auditorium, Curris Business Building, University of Nothern Iowa
Presentation Type
Open Access Poster Presentation
Document Type
poster
Abstract
This project explores the investment casting method by varying the pattern-making approach, utilizing 3D printing of PMMA patterns instead of traditional wax or injected polymer patterns to reduce pattern-making costs. The process involves printing the PMMA pattern from a CAD design and manually applying a thin wax coating to enhance the surface finish. The ceramic shell is created using a fused silica and colloidal silica slurry, with a fine silica sand coating until the shell reaches an approximate thickness of 5/16 inches. A specialized robotic system is used for the ceramic coating process, making it faster and easier than traditional methods. The pattern is then melted using a pre-heating furnace, leaving the ceramic shell mold ready for molten metal pouring. This practice demonstrates the benefits of using 3D-printed patterns, such as improved surface finishes and the ability to create more complex patterns through 3D modeling, while also recognizing the time savings achieved through the use of robotic and automated machinery.
Start Date
26-7-2024 11:00 AM
End Date
26-7-2024 1:30 PM
Event Host
Summer Undergraduate Research Program, University of Northern Iowa
Faculty Advisor
Bert Cantu
Department
Department of Applied Engineering and Technical Management
Copyright
©2024 Aini B. Constancio, Ana S. Martinez, Devani Gutierrez, Lesly M. Rubio, Mario Garcia, Rodrigo Molina
File Format
application/pdf
Recommended Citation
Constancio, Aini B.; Martinez, Ana S.; Gutierrez, Devani; Rubio, Lesly M.; Garcia, Mario; and Molina, Rodrigo, "Additive Manufacturing: Investment Casting Prototype Pantera Using 3D Printed PMMA Pattern" (2024). Summer Undergraduate Research Program (SURP) Symposium. 27.
https://scholarworks.uni.edu/surp/2024/all/27
Additive Manufacturing: Investment Casting Prototype Pantera Using 3D Printed PMMA Pattern
John Deere Auditorium, Curris Business Building, University of Nothern Iowa
This project explores the investment casting method by varying the pattern-making approach, utilizing 3D printing of PMMA patterns instead of traditional wax or injected polymer patterns to reduce pattern-making costs. The process involves printing the PMMA pattern from a CAD design and manually applying a thin wax coating to enhance the surface finish. The ceramic shell is created using a fused silica and colloidal silica slurry, with a fine silica sand coating until the shell reaches an approximate thickness of 5/16 inches. A specialized robotic system is used for the ceramic coating process, making it faster and easier than traditional methods. The pattern is then melted using a pre-heating furnace, leaving the ceramic shell mold ready for molten metal pouring. This practice demonstrates the benefits of using 3D-printed patterns, such as improved surface finishes and the ability to create more complex patterns through 3D modeling, while also recognizing the time savings achieved through the use of robotic and automated machinery.